ME 4233/6233 Fundamentals of FEA
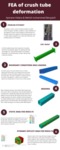
Files
Download presentation (85.4 MB)
Loading...
Description
In this research paper, finite element methods will be implemented to analyze the crush tube deformation. It will be modeled as a classic nonlinear problem on which mesh convergence, boundary conditions, contact techniques are investigated. The finite element software ABAQUS will be used to perform FE simulation of the crushing of a tube between two flat plates under axial compressive load and the geometry used is a thin-walled rectangular cross section tube. Project deliverables for this work include the crush response of the tube with mesh sensitivity study to accurately model the buckling mode and load displacement characteristics. Mesh density and uniformity on the structure were also investigated. Other deliverables include boundary conditions versus the load applied and effects of omitting contact for buckling problem, starting with an elastic model, and then comparing it to other plasticity models in terms of strain rate and temperature dependency ABAQUS implicit versus standard solvers were both used to compare the computational time requirements, ease of convergence and contact implementation.In this research paper, finite element methods will be implemented to analyze the crush tube deformation. It will be modeled as a classic nonlinear problem on which mesh convergence, boundary conditions, contact techniques are investigated. The finite element software ABAQUS will be used to perform FE simulation of the crushing of a tube between two flat plates under axial compressive load and the geometry used is a thin-walled rectangular cross section tube. Project deliverables for this work include the crush response of the tube with mesh sensitivity study to accurately model the buckling mode and load displacement characteristics. Mesh density and uniformity on the structure were also investigated. Other deliverables include boundary conditions versus the load applied and effects of omitting contact for buckling problem, starting with an elastic model, and then comparing it to other plasticity models in terms of strain rate and temperature dependency ABAQUS implicit versus standard solvers were both used to compare the computational time requirements, ease of convergence and contact implementation. An adiabatic simulation will be added using Johnson-Cook method.
Keywords
Crush tube, Stress-strain curve, Displacement, Dynamic analysis, Johnson-Cook, Adiabatic
Disciplines
Engineering | Mechanical Engineering
College
James Worth Bagley College of Engineering
Department
Department of Mechanical Engineering
Recommended Citation
BENYAICH, Mohammed El Mehdi Mr and HIDARA, Aymane Mr, "Finite Element Modeling of Crush Tube Deformation" (2022). ME 4233/6233 Fundamentals of FEA. 35.
https://scholarsjunction.msstate.edu/fea/35
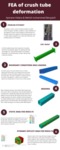